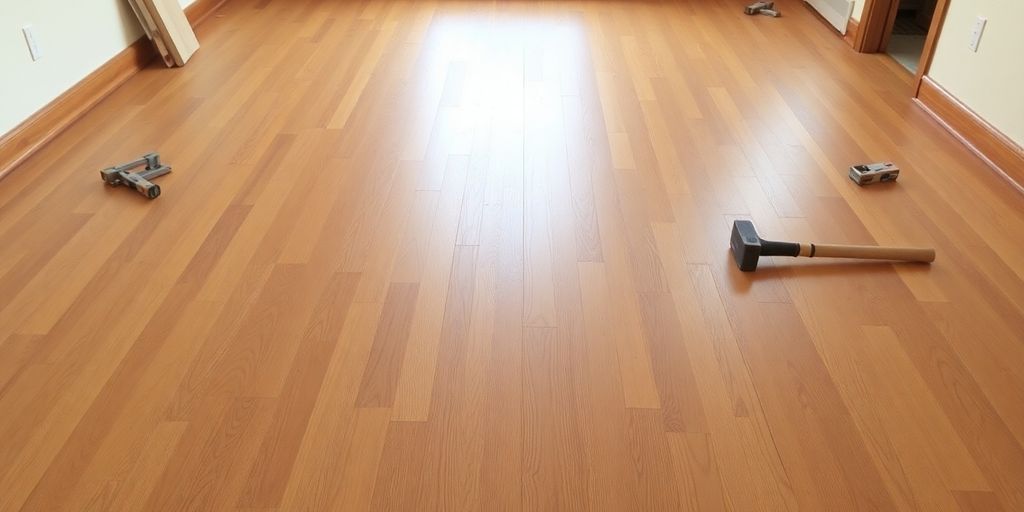
Step-by-Step Guide on How to Lay Hardwood Flooring Like a Pro
Preparation: Tools And Materials Needed

Alright, so you're thinking about laying some hardwood flooring yourself? Awesome! But before you even think about swinging a hammer, let's make sure you've got all your ducks in a row. Trust me, nothing's worse than getting halfway through a project and realizing you're missing something crucial. It's happened to me more times than I care to admit. So, let's break down what you'll need.
Gathering Essential Tools
Okay, tools first. This isn't just about having any tools; it's about having the right tools. You could technically try to install hardwood with a butter knife and a dream, but I wouldn't recommend it. Here's a list to get you started:
- Tape Measure: You'll need this for, well, measuring everything. Get a good one that won't snap after two uses.
- Chalk Line: Snapping straight lines is key, especially for your first row. A chalk line makes this a breeze.
- Pry Bar: For gently removing baseboards without destroying them. Unless you want to replace them, of course.
- Flooring Nailer: This is a big one if you're nailing down your floor. Makes the job way faster and more secure. You can rent these if you don't want to buy one.
- Saw: A miter saw is ideal for clean, accurate cuts, but a jigsaw can work in a pinch, especially for tricky angles.
- Rubber Mallet and Tapping Block: These help you fit the boards together snugly without damaging the edges. Trust me, you'll need these.
- Spacer Blocks: Maintaining consistent expansion gaps around the perimeter is super important. Spacers make it easy.
- Shop Vac: Keeping the subfloor clean is a must. A shop vac is way more effective than a regular vacuum.
- Safety Gear: Don't skimp on this! Gloves, knee pads, and safety glasses are non-negotiable. Your body will thank you.
Selecting The Right Hardwood
Choosing the right hardwood is more than just picking a color you like. There are a few things to consider:
- Solid vs. Engineered: Solid hardwood is, well, solid wood. Engineered hardwood has a thin layer of real wood on top of a plywood core. Engineered is more stable in humid environments.
- Wood Species: Different species have different hardness levels. Oak and maple are popular, durable choices. Softer woods like pine are more prone to dents and scratches.
- Grade: Hardwood is graded based on its appearance. Higher grades have fewer knots and imperfections, but they're also more expensive.
- Finish: Pre-finished flooring is convenient, but unfinished flooring lets you customize the stain and finish. Consider the pros and cons of each.
Here's a quick table comparing some popular hardwood species:
Species | Hardness (Janka) | Pros | Cons |
---|---|---|---|
Red Oak | 1290 | Durable, readily available, relatively affordable | Can be sensitive to moisture |
White Oak | 1360 | More water-resistant than red oak, classic look | Slightly more expensive than red oak |
Maple | 1450 | Very hard and durable, smooth grain | Can be difficult to stain evenly |
Hickory | 1820 | Extremely durable, rustic look | Can be very expensive |
Bamboo | Varies | Sustainable, unique look, can be very hard depending on construction | Quality varies widely, some types are prone to scratching and denting |
Preparing The Subfloor
Your subfloor is the foundation of your entire flooring project, so don't skip this step! A poorly prepared subfloor can lead to squeaks, unevenness, and even premature failure of your new floor.
Here's what you need to do:
- Clean it: Vacuum and sweep the subfloor thoroughly to remove all dust, dirt, and debris. A clean surface is essential for proper adhesion.
- Inspect for Damage: Look for any signs of water damage, rot, or mold. Address any issues before proceeding. Ignoring these problems will only cause bigger headaches down the road.
- Level it: Use a long level or straightedge to check for any dips or high spots. Sand down high spots and fill in low spots with a leveling compound. The flatter, the better.
- Check Moisture Levels: Use a moisture meter to check the moisture content of both the subfloor and the hardwood flooring. Make sure they're within the recommended range. Too much moisture can cause the wood to warp or buckle. You might need backsplash tile installation if there is too much moisture.
I can't stress enough how important subfloor preparation is. I once rushed this step on a project, and the floor ended up looking like a roller coaster. Seriously, don't make the same mistake I did. Take your time and do it right.
Understanding The Installation Process
Choosing The Right Installation Method
Okay, so you've got your hardwood, you've got your tools, now it's time to figure out how you're actually going to put this floor down. There are a few main ways to install hardwood, and the best one for you depends on your subfloor, the type of hardwood you chose, and honestly, your comfort level with DIY projects. Let's break down the common methods:
- Nail-Down: This is where you literally nail the wood to the subfloor. It's best for solid hardwood and requires a wood subfloor. You'll need a special flooring nailer for this. It's pretty secure, but can be a bit noisy.
- Glue-Down: As it sounds, you glue the hardwood directly to the subfloor. This works well for concrete subfloors and some engineered hardwoods. You'll need to use the right kind of adhesive, and it can be a bit messy. Make sure you hire Echo Tile and Stone for a professional installation.
- Floating: This method involves clicking the planks together to form a
Step-By-Step Installation Guide
Installing The First Row
Okay, so you've prepped everything, and you're ready to actually start laying down some wood. Exciting! The first row is arguably the most important, so take your time and get it right. It's the foundation for everything else.
- Start by laying out your first row along the longest, straightest wall in the room. Use spacers between the wall and the boards to maintain that crucial expansion gap. We talked about that earlier, right? Don't skip it!
- Make sure the groove side of the plank is facing the wall. This will make it easier to attach the next rows.
- Pre-drill pilot holes if you're nailing or screwing. This prevents the wood from splitting, especially near the ends.
- Use a level to ensure your first row is perfectly straight. Any deviation here will amplify down the line, and you'll end up with a wonky floor. Nobody wants that.
Continuing Row By Row
Alright, first row's down! Now the fun really begins. This is where you start to see the floor actually taking shape. Just keep at it, row by row.
- Stagger the end joints of the planks. This not only looks better but also adds strength to the floor. Aim for at least a six-inch difference between the joints on adjacent rows. Trust me, it makes a difference.
- Use a tapping block and a mallet to gently tap the planks together. You want a snug fit, but don't go crazy and damage the edges. Gentle is key.
- Check your alignment every few rows. It's easier to make small adjustments along the way than to fix a major problem later. A chalk line can be your best friend here.
- Don't forget those expansion gaps! Keep using spacers along the walls as you go. It's easy to get caught up in the process and forget, but future you will thank you.
Finishing The Last Row
Almost there! You're probably starting to feel like a pro at this point. But don't let your guard down just yet. The last row can be a bit tricky, but you've got this.
- Measure the space for the last row carefully. Chances are, you'll need to cut the planks to fit. Use a table saw or a circular saw for clean, accurate cuts.
- Remember to account for the expansion gap! You might need to rip the planks lengthwise to get the right width.
- Use a pull bar to help you snug the last row into place. Space can be tight against the wall, and a pull bar gives you the leverage you need.
- Install any transition pieces or thresholds. These are those little strips that cover the gaps between different types of flooring, or at doorways. Your hardwood flooring retailer can help you pick the right ones. Now, install whatever baseboard or shoe molding you choose, and you are finished with this project!
I remember when I did my first hardwood floor. I thought the last row would be a breeze, but it ended up being the most frustrating part. I had to recut several planks because I didn't measure correctly. Lesson learned: measure twice, cut once!
Tips For Achieving A Professional Finish
Staggering Joints
Okay, so you're laying down your hardwood flooring, and you want it to look like it was done by a pro, right? One of the biggest things that separates a good job from a great job is how you stagger the joints. Basically, you don't want the ends of your boards lining up in a predictable pattern.
Here's why it matters:
- It looks way better. A random pattern looks more natural and less like a cheap laminate. Think of it like bricklaying – you wouldn't stack bricks directly on top of each other, would you?
- It makes the floor stronger. Staggered joints distribute weight better, so you're less likely to get weak spots or squeaks down the road.
- It hides imperfections. If your boards aren't perfectly straight (and let's be honest, they probably aren't), staggering helps to mask those little wobbles.
Maintaining Expansion Gaps
Expansion gaps are super important. I know, they can be annoying because they leave a little space around the edges of the room, but trust me, you need them. Wood expands and contracts with changes in temperature and humidity. If you don't leave room for that movement, your floor could buckle or warp. Not good.
Here's the deal:
- Always check the manufacturer's instructions for the recommended gap size. Usually, it's around 1/4 to 3/8 of an inch.
- Use spacers along the walls while you're installing the floor to maintain that gap. You can buy these at any home improvement store, or you can just use small pieces of wood or shims.
- Don't skip this step! I know it's tempting to just butt the boards right up against the wall, but you'll regret it later.
I remember one time, my buddy Dave decided to ignore the expansion gap rule. He thought he knew better. A few months later, his floor started to buckle in the middle of the living room. He had to rip up half the floor and start over. Learn from Dave's mistakes, people.
Applying Finishing Touches
Alright, you've laid the floor, and it looks pretty good. But it's the little things that really make a difference. Here are a few finishing touches to consider:
- Install baseboards or quarter-round molding. This covers up the expansion gap and gives the floor a clean, finished look. Make sure to nail the molding to the wall, not the floor, so the floor can still move freely.
- Use a wood filler to fill any small gaps or imperfections. You can find wood filler that matches the color of your floor at most hardware stores. Just apply it with a putty knife, let it dry, and sand it smooth.
- Clean the floor thoroughly. Use a damp mop and a wood floor cleaner to remove any dust or debris. Avoid using too much water, as this can damage the wood.
- Consider applying a coat of polyurethane. This will protect the floor from scratches and wear and tear. If you do this, make sure to follow the manufacturer's instructions carefully.
Post-Installation Care And Maintenance

So, you've got your beautiful new hardwood floor installed. Awesome! But the work doesn't stop there. Keeping it looking great for years to come means taking good care of it. Think of it like a pet – it needs regular attention to stay happy and healthy. Here's the lowdown on how to do just that.
Cleaning The New Floor
Okay, first things first: cleaning. Don't just grab any old cleaner. Hardwood needs special treatment.
- Wait a few days before the first cleaning: Give the finish time to fully cure. Usually, 3-5 days is a safe bet.
- Use a microfiber mop: These are gentle and effective at picking up dust and dirt without scratching the surface.
- Choose a pH-neutral hardwood floor cleaner: Avoid anything acidic or alkaline, as these can damage the finish. I usually go for the ones specifically made for hardwood; they're easy to find at most stores.
- Vacuum regularly: Use a vacuum with a soft brush attachment to prevent scratches. I do this once a week, sometimes more if I've been tracking in a lot of dirt.
Applying Protective Coatings
Think of protective coatings as sunscreen for your floor. They help shield it from wear and tear, keeping it looking newer for longer. There are a few options, and what you choose depends on your lifestyle and how much effort you want to put in.
- Polyurethane coatings: These are super durable and offer great protection against scratches and spills. They're a good choice for high-traffic areas. You can find porcelain tile options that are durable and easy to clean.
- Wax coatings: These give a nice, natural look but require more maintenance. You'll need to re-wax every few months to keep the floor protected.
- Aluminum Oxide Finishes: Some prefinished floors come with this. It's incredibly tough and long-lasting, but you can't reapply it yourself. It's done at the factory.
Regular Maintenance Tips
Regular maintenance is key to keeping your hardwood floor in tip-top shape. It's all about preventing damage before it happens.
- Use rugs in high-traffic areas: Entryways, hallways, and areas in front of sinks are prime spots for rugs. They'll catch dirt and moisture before they reach the floor.
- Place felt pads under furniture: This is a game-changer. Felt pads prevent scratches when you move chairs, tables, and other furniture around. I put them on everything!
- Trim your pets' nails: Long nails can scratch the floor. Keep them trimmed to minimize damage.
- Clean up spills immediately: Don't let spills sit on the floor. Wipe them up right away to prevent staining and water damage.
A little bit of prevention goes a long way. By following these simple maintenance tips, you can keep your hardwood floor looking beautiful for years to come. It's worth the effort to protect your investment and enjoy your gorgeous floors for a long time.
Common Mistakes To Avoid
So, you're almost done, huh? Well, before you pop that champagne, let's talk about some common pitfalls I've seen people stumble into when laying hardwood. Trust me, a little foresight can save you a ton of headache (and money) down the road.
Ignoring Acclimation
Okay, I can't stress this enough: don't skip the acclimation period! I know, you're excited to get that new floor down, but wood is a natural material, and it needs time to adjust to the humidity levels in your home. If you install it right away, you might end up with gaps or buckling later on. It's like rushing a good recipe – you just can't do it.
- Let the wood sit in the room where it will be installed for at least 3-5 days. Some pros even say a week or two is better.
- Keep the boxes open to allow air to circulate around the planks.
- Make sure the room's temperature and humidity are at normal living conditions.
Neglecting Subfloor Preparation
Your subfloor is the foundation of your new hardwood floor, so don't skimp on the prep work. Any imperfections will telegraph through the hardwood, leading to an uneven and potentially squeaky floor. I've seen people try to cut corners here, and it always comes back to bite them.
- Make sure the subfloor is level. Use a self-leveling compound if needed.
- Check for moisture. You don't want to trap moisture under your new floor.
- Clean the subfloor thoroughly. Remove any debris, nails, or screws.
I remember this one time, my buddy Dave decided to install hardwood in his basement without checking the moisture levels. A few months later, his floor started cupping like crazy. He had to rip it all out and start over. Talk about a costly mistake!
Improper Layout Planning
Failing to plan is planning to fail, right? That's especially true when it comes to laying hardwood. You need to think about the direction of the planks, where you'll start, and how you'll handle transitions. A little planning can make a big difference in the final result. Consider flooring installation to avoid these issues.
- Think about the longest, straightest wall to start from.
- Consider the light source and how it will affect the look of the floor.
- Stagger the end joints of the planks to avoid unsightly patterns. Avoid H-seams by staggering each joint by at least 6 inches. This prevents weak spots and creates a more visually appealing, natural look.
Here's a quick table to illustrate the importance of staggering:
Staggering Distance | Structural Integrity | Aesthetic Appeal |
---|---|---|
None | Weak | Poor |
Less than 6 inches | Moderate | Fair |
6 inches or more | Strong | Good |
Tools For Troubleshooting
So, you've laid your hardwood floor, and something isn't quite right? Don't panic! Most issues are fixable with a bit of know-how and the right tools. Let's walk through some common problems and how to tackle them.
Identifying Common Issues
Okay, first things first: what's actually wrong? Is it squeaking, buckling, or are there gaps forming? Pinpointing the problem is half the battle. Here's a quick rundown of common hardwood floor issues:
- Squeaking: Often caused by subfloor issues or loose nails.
- Buckling: Usually due to moisture problems.
- Gapping: Can happen when the wood wasn't properly acclimated or humidity levels fluctuate.
- Cupping: Edges of the boards are higher than the center, also moisture-related.
- Crowning: Center of the boards are higher than the edges.
Using Repair Kits
For minor scratches, dents, or small gaps, repair kits can be a lifesaver. These kits usually include wood filler, color-matching putty, and sometimes even touch-up markers. Here's how to use them:
- Clean the affected area thoroughly.
- Apply the wood filler or putty to the damaged spot.
- Let it dry completely according to the manufacturer's instructions.
- Sand it smooth, being careful not to damage the surrounding finish.
- Use a touch-up marker to blend the repair with the rest of the floor. For larger gaps, you might need wood shims and wood glue.
When To Call A Professional
Okay, sometimes you've just gotta admit defeat. If you're dealing with major buckling, widespread squeaking that you can't trace, or any kind of structural issue, it's time to call in the pros. Think of it this way: you don't want to make the problem worse by trying to fix something beyond your skill level. Plus, a professional can often diagnose the root cause of the issue and prevent it from happening again. For example, shower tile installation experts can help identify moisture issues that might be affecting your hardwood floor.
Knowing when to DIY and when to call a professional is key to maintaining your hardwood floors. It can save you time, money, and a whole lot of frustration in the long run.
When things go wrong with your flooring, having the right tools can make all the difference. From simple fixes to more complex issues, knowing what to use can help you solve problems quickly. Don’t let flooring troubles stress you out! Visit our website for helpful tips and tools that can guide you through any flooring challenge you face.
Check out our resources to get started!
Wrapping It Up
So there you have it! Laying hardwood flooring isn’t just for the pros. With some patience and the right tools, you can totally do it yourself. Sure, it might take a bit of time and effort, but the satisfaction of seeing your new floor come together is worth it. Just remember to take your time, measure twice, and don’t rush the finishing touches. If you hit a snag, don’t hesitate to ask for help or look up a quick video. In the end, you’ll have a beautiful floor that you can be proud of. Happy flooring!